提高棒材定尺率生產實踐
摘要:介紹了攀鋼金屬制品有限公司棒材生產線提高定尺率的生產實踐,通過控制加熱爐氧化燒損、負偏差精度及切分規(guī)格線差控制、倍尺剪切精度提升、齊頭棍道改進、各規(guī)格鋼坯定長等措施,棒材定尺率由開始平均約96%?97%逐步提高到99.2%?99.3%。
攀鋼集團攀枝花金屬制品有限公司棒材生產線由成都原樣利舊搬遷到攀枝花,投產之初平均定尺率約為96%?97%。非定尺鋼材與定尺鋼材價差較大,非定尺市場銷售困難,為此大程度地提高定尺率成為攻關的課題之一。通過對影響定尺率的軋鋼工序進行全面梳理,分析產生非定尺的原因,采取倍尺剪切精度控制、齊頭輻道改進、軋制規(guī)格精確控制、切分規(guī)格線差控制、嚴格加熱工藝控制、鑄坯定長等系列措施,定尺率逐步提高到99.2%?99.3%,成材率也得到了提高。
1、棒材生產線簡介
根據攀鋼產線結構調整需求,攀鋼集團利舊搬遷閑置設備,在攀枝化本部建設一條年產60萬噸的棒材生產線。棒材生產線于2017年3月1日熱負荷試車。棒材產品規(guī)格為C>12 mm?C>40 mm的帶肋鋼筋,其中012 mm規(guī)格采用三切分軋制,①14mm?©18 mm規(guī)格采用兩切分軋制,其余規(guī)格為單線軋制。主要裝備由1臺蓄熱推鋼式加熱爐、18架軋機、3臺飛剪、1臺冷剪機、1臺步進齒式冷床、檢查收集設備等組成。有關工藝平面布置示意圖如圖1所示。
2、影響定尺率因素及改進措施
2.1 、3號倍尺剪剪切精度
棒材生產線3號倍尺飛剪安裝在18 #精軋機組后面,作用為將軋制后的成品棒材按要求分段剪切成符合規(guī)定的倍尺長度,方便冷床收集和緩冷。3號倍尺飛剪的剪切精度是直接影響定尺率的重要因素。由于成品棒材通過3號飛剪速度約16 m/s,這就要求3號飛剪的控制必須快速、及時、 準確。實際生產中發(fā)現3號飛剪倍尺長度剪切不穩(wěn)定,同樣的倍尺長度,每根鋼材的長度變化大,造成切頭尾浪費大,嚴重影響定尺率。
3號飛剪倍尺剪切精度是由熱金屬檢測儀控制啟動,按設定軋制速度進行倍尺長度剪切,沒有進行軋件實際速度的測量。同時飛剪啟動檢測元件受現場環(huán)境制約,抗干擾能力差,常發(fā)生不切、切長等現象,對定尺率影響較大。為此修改控制邏輯,通過終軋電機實際轉速與軋輻工作輻徑計算軋件線速,以此作為軋件實際線速度E,然后賦予人工修正窗口進行修正,完成實際定尺長度計算,滿足倍尺動作測量長度要求。對飛剪啟停時間誤差改進,采用專業(yè)的高速型號接近開關,確保剪刃位置達到精確定位目的,減少剪刃啟停造成的切頭長度變化。在冷床末端增設攝像頭,觀察鋼在冷床齊頭輻道齊頭后末端長度情況,并在監(jiān)控上劃線警示,對成品倍尺長度進行監(jiān)控,避免設備故障引起的非尺量擴大。
2.2、冷床齊頭輻道改進
投產之初,棒材在齊頭輻道上齊頭效果不好,尤其是切分小規(guī)格帶肋鋼筋齊頭不好。當對齊輻道主動輻較多時,小規(guī)格由于剛性差,倍尺棒材撞到擋板后產生拱彎;當對齊輻道主動輻較少時,對齊輻道上先撞到擋板的棒材立即停止,未撞到擋板的棒材因動力不足前進遲緩無法齊頭。對齊輻道速度設置不當,也會產生拱彎或無法齊頭現象。為此齊頭輻道的一個重要機理是:當倍尺棒材撞到擋板時要實現可靠地打滑,確保倍尺棒材與齊頭輻道之間的摩擦力不會過大図。
原齊頭輻子采用凹槽結構,其左側輻面60度斜角,右側輻面34度,底部輻面水平段很窄,切分鋼筋與輻面呈多點接觸,切分生產的兩支帶肋鋼筋形成重疊,摩擦阻力加大,不易實現可靠的打滑。為此將左側60度斜角改成垂直,增大輻子底部直線段長度,增大鋼筋之間空隙,減少鋼筋與輻道之間的摩擦阻力,有關修改前后示意圖如圖2、圖3所示。此齊頭輻道結構改進后,齊頭效果得到了較大的改善。另對操作室HMI監(jiān)控畫面進行優(yōu)化,增加齊頭輻道速度控制對話框,主操人員可在HMI監(jiān)控畫面上適時修改齊頭輻道運行速度,實現不同規(guī)格棒材之間輻道速度可控,保證主動輻前進動力可調,基本杜絕了鋼筋不能齊頭的現象。
2.3、嚴格負偏差精度控制
同一成品規(guī)格尺寸的帶肋鋼筋,相同的鋼坯長度,由于尺寸精度不同,軋制出的成品長度會有不同,這也會對定尺率造成影響。結合棒材帶肋鋼筋的市場用戶需求,我廠對帶肋鋼筋實行負偏差控制O從孔型設計、軋槽加工、軋機裝配精度、料型標準化作業(yè)、負偏差目標值、定捆定支、捆包重量預警等各個方面開展工作,以此嚴格負偏差控制精度。
控制負偏差主要是控制好內徑,對整個成品基圓實行負偏差設計。為保證軋槽的使用壽命,軋槽橫肋加工深度按照大正公差0.1?0.2 mm進行加工。對各道次料型實行標準化作業(yè),制作料型展板與記錄展板,要求班組人員嚴格按標準料型進行控制,每班對料型進行抽查,并將抽查的料型尺寸記錄在展板上。嚴格軋機裝配精度,訂購12臺短應力新軋機,新軋機可保證軋機徑向間隙控制在0.2 mm以內,軸向間隙控制在0.1 mm以內,整個軋機彈跳小,重量偏差可穩(wěn)定控制在±0.5%以內。在取樣方面,配備專用的樣品測量及稱重工具,規(guī)范取樣頻次、測量方法等。對各規(guī)格進行定捆定支,規(guī)定捆包重量偏差內控上下限,各崗位通過MES系統(tǒng)可適時監(jiān)控捆包重量,起到捆重預警的作用,方便軋鋼工及時調整成品尺寸,保證尺寸精度的穩(wěn)定。
2.4、嚴格切分線差控制
軋制帶肋鋼筋切分規(guī)格①12 mm?©18 mm,成品幾何尺寸存在較大線差時,既影響到產品質量的穩(wěn)定,又增加定尺剪切時的切頭尾長度,導致非定尺量的增加。在嚴格切分線差的控制上,除強化軋輻加工精度、軋槽使用周期、軋機裝配質量與導衛(wèi)對中外。優(yōu)化切分規(guī)格14架立箱孔型,槽底增加凸度, 降低軋槽磨損程度。切分導衛(wèi)切分輪由原單側固定改為雙側固定,降低切分輪軸向竄動產生的故障。開軋前用鐵絲通過軋輻兩側輻縫,保證兩側輻縫偏差控制在0.1 mm以內。在控制兩側輻縫差的時候,剛開始職工較為忽略13架平輻,經過一段時間的生產發(fā)現,軋件在13架平輻中自由寬展,保證軋輻南北輻縫一致是關鍵,否則軋件會出現楔形,影響14架箱形孔的充滿程度。通過一系列的技術改進與強化管理,切分規(guī)格線差基本可控制在100 mm以內。
2.5、嚴格控制切頭尾長度
在保證缺陷切凈與不造成軋線堆鋼的情況下, 制定不同規(guī)格1井飛剪切頭、2井飛剪切頭尾及冷剪切頭尾長度。操作工根據1井、2#飛剪前軋機的線速度和料型尺寸,設定對應飛剪的超前系數和剪切長度,并根據實際情況設定飛剪的剪切補償,把切頭尾長度降到要求范圍,減少過程金屬的損失,穩(wěn)定倍尺長度的控制。棒材各規(guī)格的1井、2井飛剪及冷剪切頭尾長度見表1。
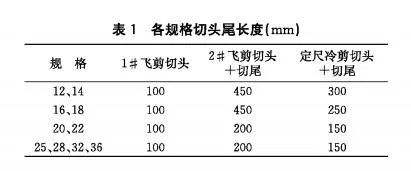
2.6、降低加熱氧化燒損
為了減少鋼坯氧化燒損,在盡可能的情況下降低鋼坯加熱溫度,實行快速加熱,縮短鋼坯在爐時間,控制氧化氣氛。同時結合設備負荷能力,鋼坯燒透,斷面溫度均勻,鋼坯尾部溫度略高于頭部30 °C,以保證軋制過程中的溫度均勻性,為獲得較高的成品定尺率奠定基礎聞。
2.7、鋼坯定長
由于煉鋼工序對鑄坯無稱重裝置,只能進行長度控制。在經過設備優(yōu)化改進、尺寸規(guī)格精確控制、 切頭精確控制、煉鋼不同澆鑄時段單重測算等基礎上,不斷對鋼坯長度進行優(yōu)化。經過前后多輪不斷優(yōu)化與調整,對不同規(guī)格鋼坯長度進行定長,達到較為好的鋼坯重量。
3、結語
通過倍尺剪切精度提升、齊頭輻道改進、負偏差精度及切分規(guī)格線差控制、切頭尾長度及氧化燒損控制、各規(guī)格鋼坯定長等措施,棒材定尺率從剛開始平均約96%?97%逐步提高到99.2%?99.3%, 成材率也得到提高,取得了好的經濟效益。